So the other day I got a nice pair of Ray Ban glasses for a very special person in my life. Since they were a gift, I decided to wrap them up. At first I thought that I should use regular wrapping paper, but then I realized I wanted to do something more interesting... I decided to use my Handibot to make a case for them. I started off drawing the box I had in mind using Sketchup:
After I got the design down, I sent it over to VCarve to make the toolpaths. VCarve now supports Sketchup import, so it's really easy to take a design like this from Sketchup and bring it into VCarve to make your toolpaths.
Once the toolpaths were made I set about clamping the pieces to the bench so I could set the Handibot on top of them for milling.
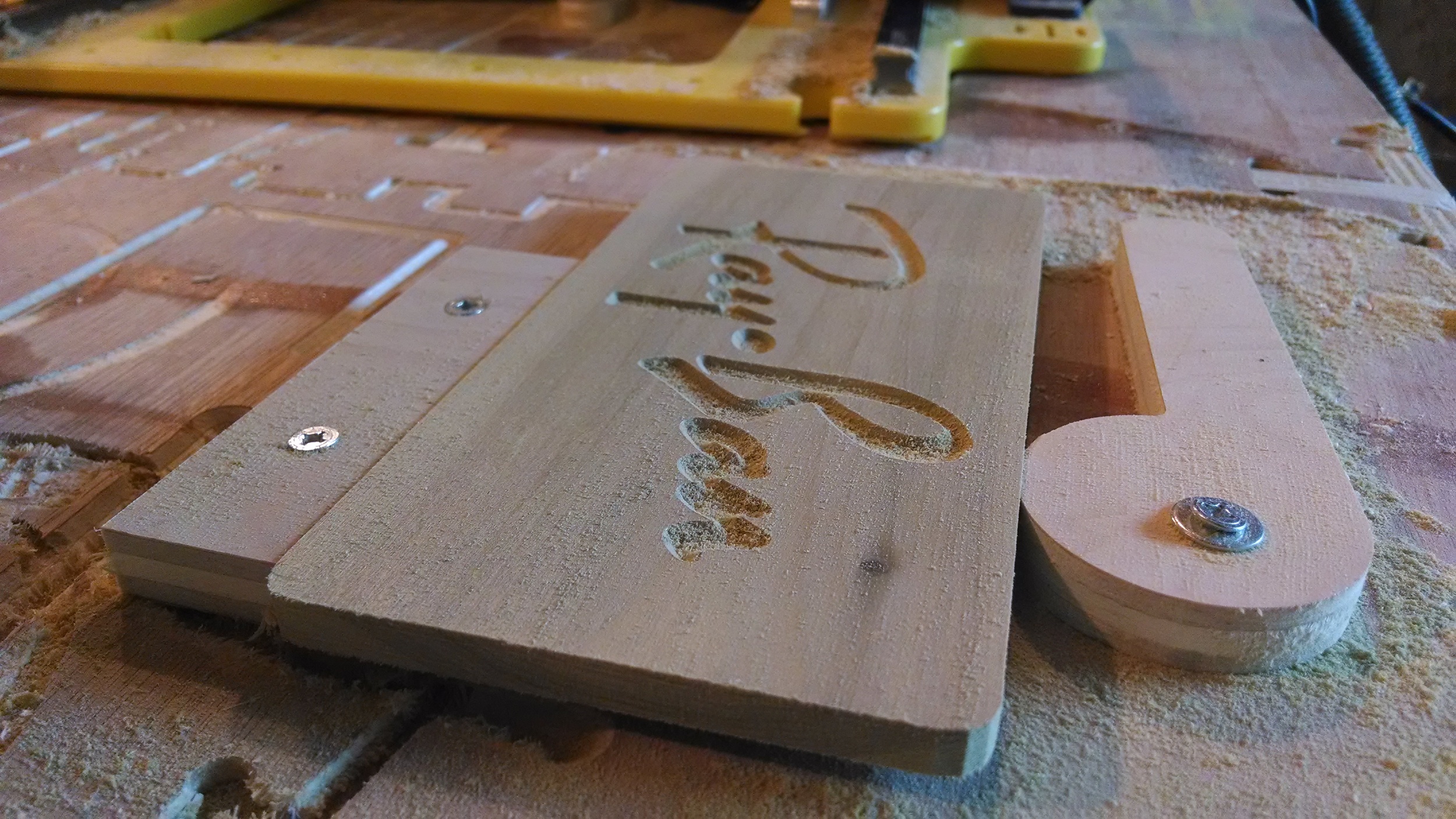
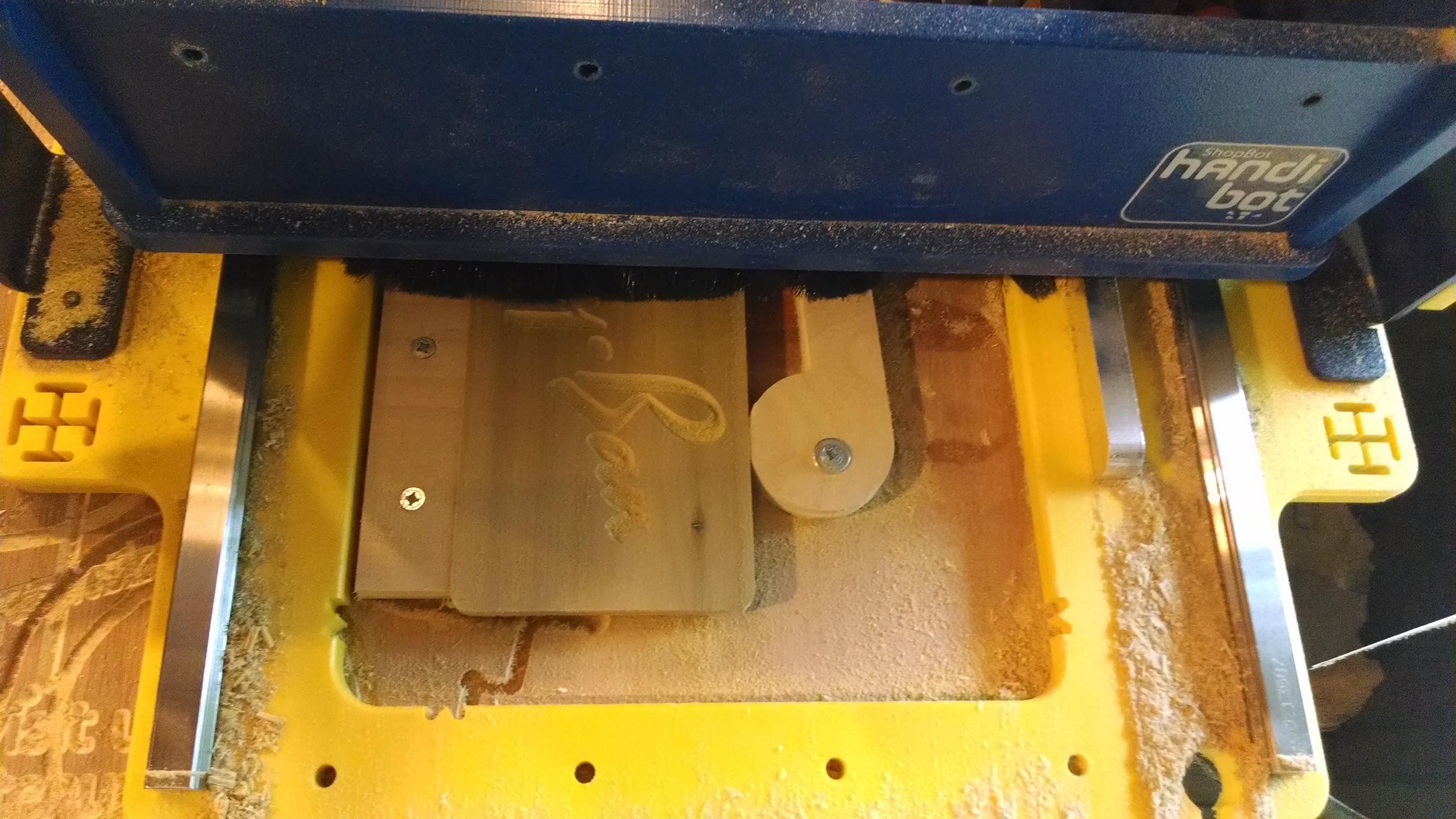
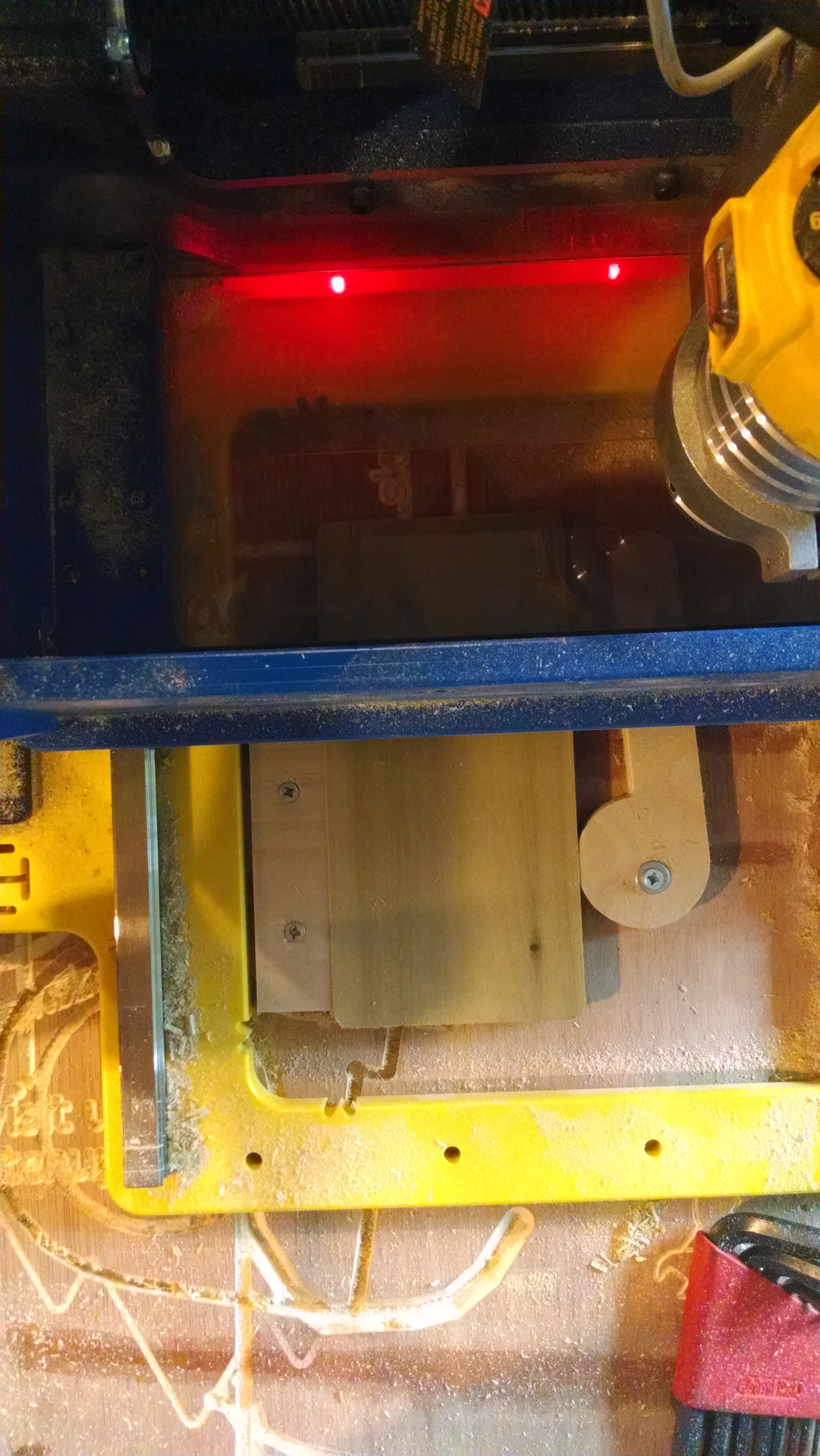
Once I had the clamping done I set about milling. The spacers and the bottom were easy. I used a typical end mill bit to cut those, and V bit for the Ray Ban logo.
You'll notice here that the logo came out "hairy". Since I was going to Shellac this case when I was done, I needed to hand sand out the letters. I didn't have the patience to do that, so I had an idea about filling the letters and sanding them smooth. Since I used to work in autobody, I decided to use some automotive body filler. I took that and mixed it with some old black paint I had laying around. After mixing it together I smeared the filler on the letters and sanded it smooth. The result is this:
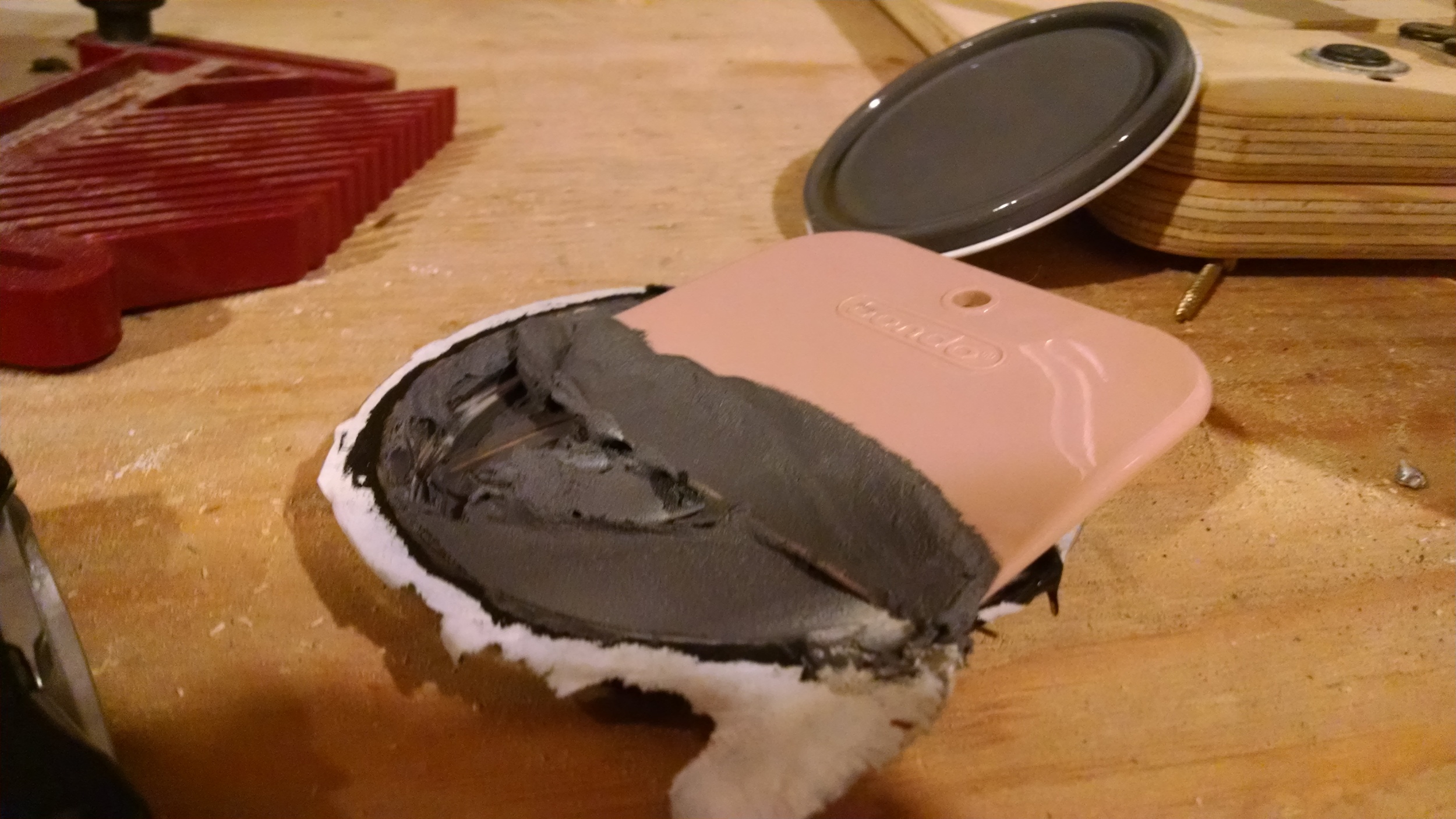
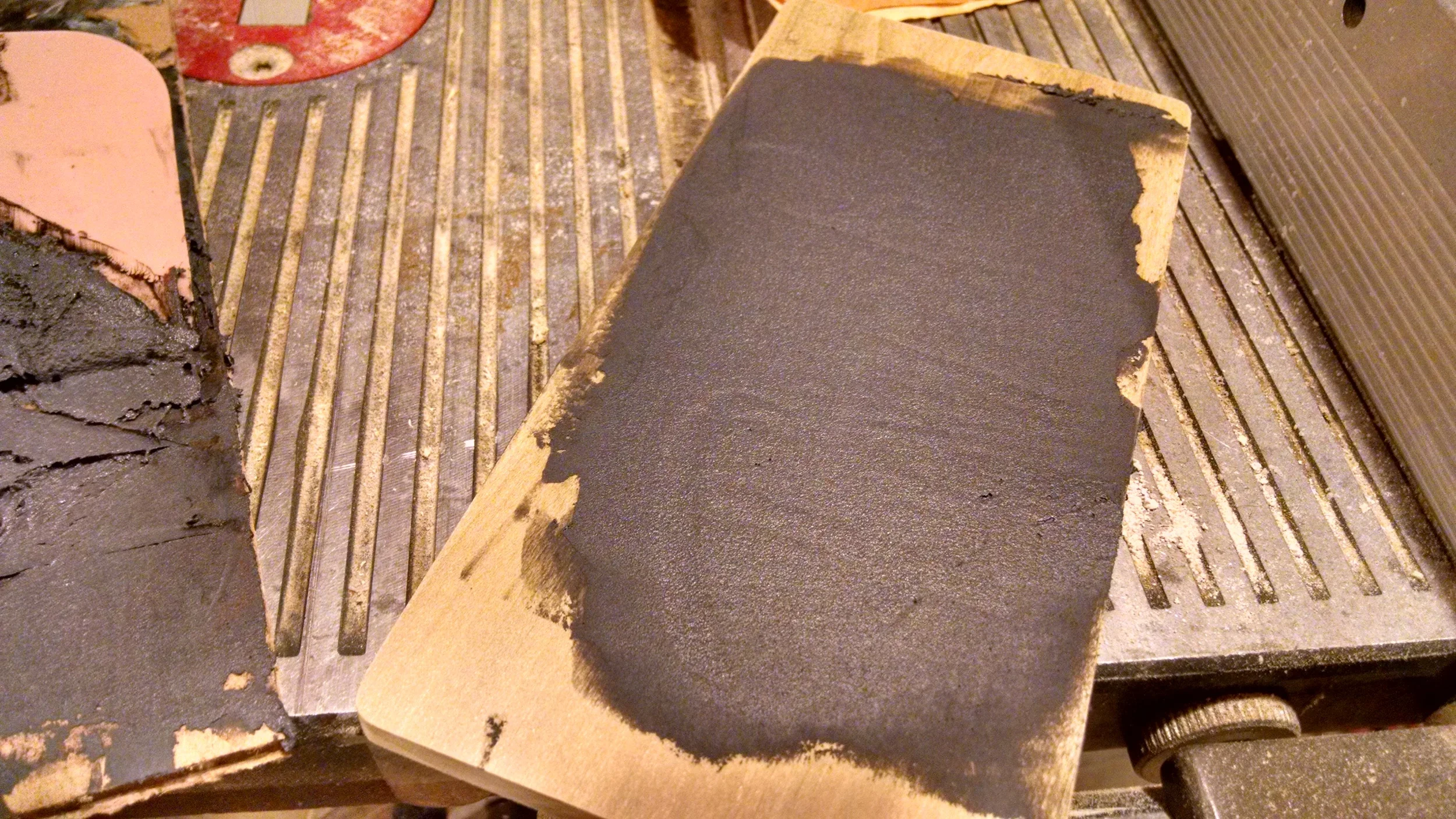
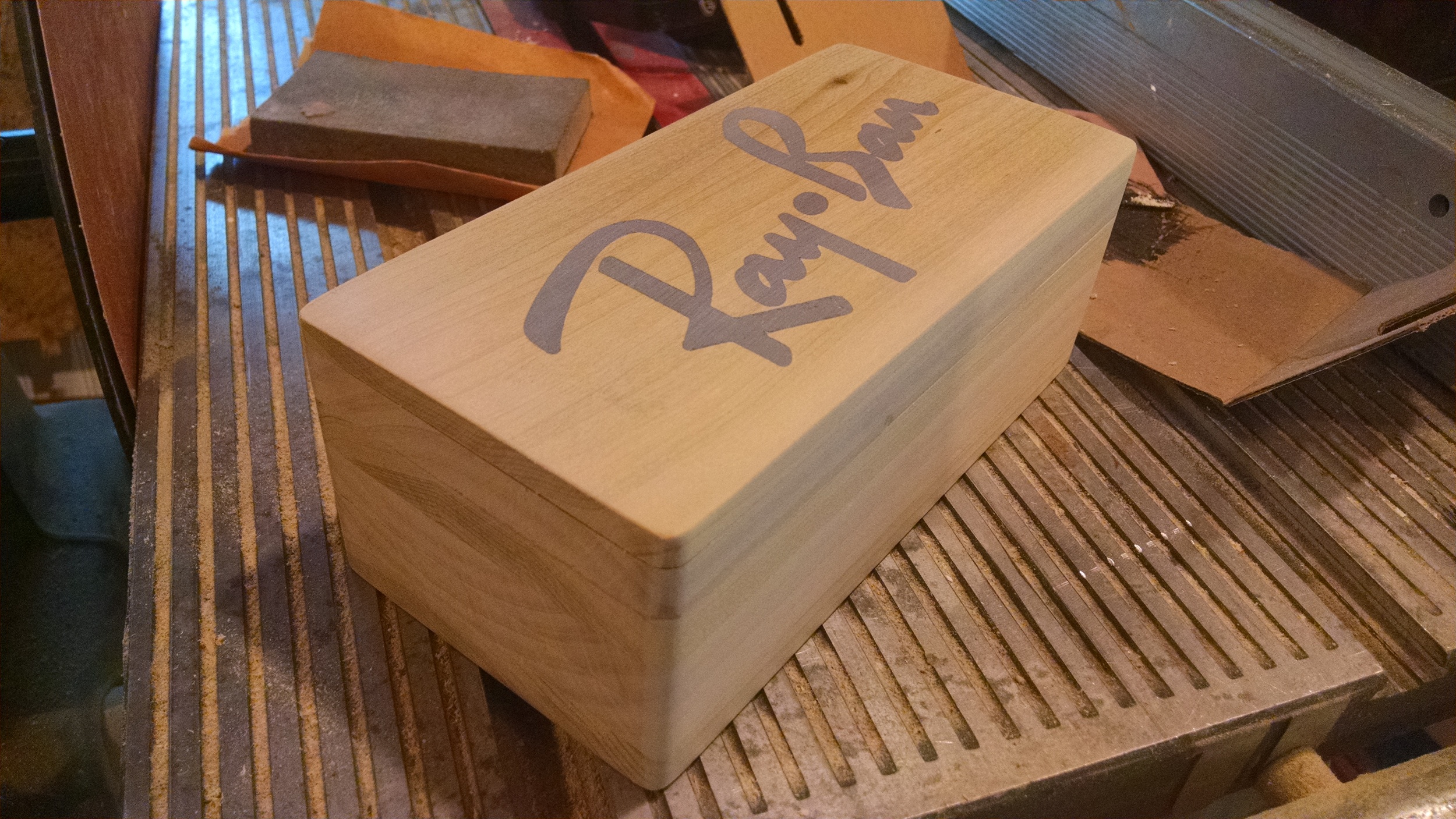
After that proved to be a success I Shellace'd the whole thing. The results were excellent.
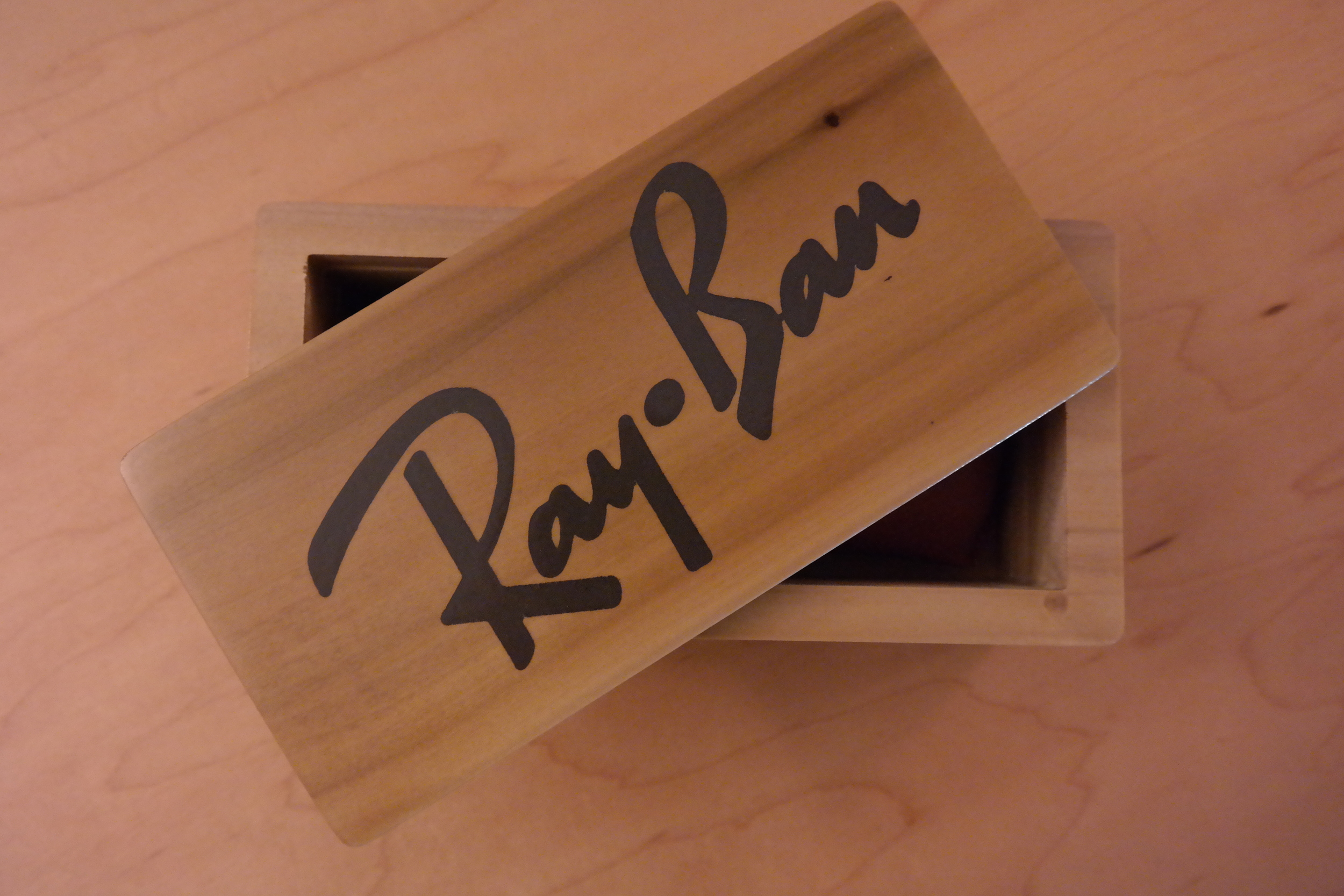
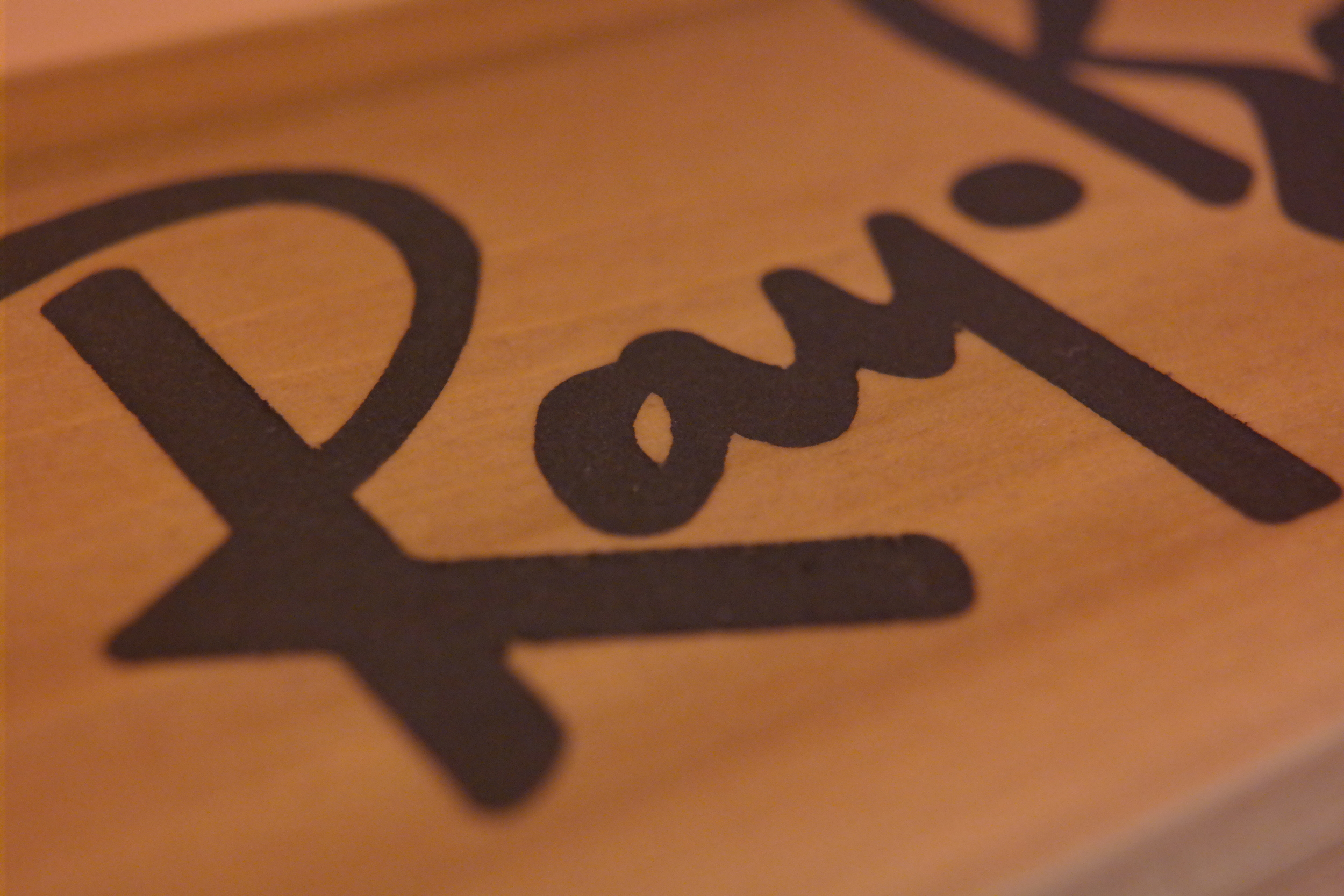
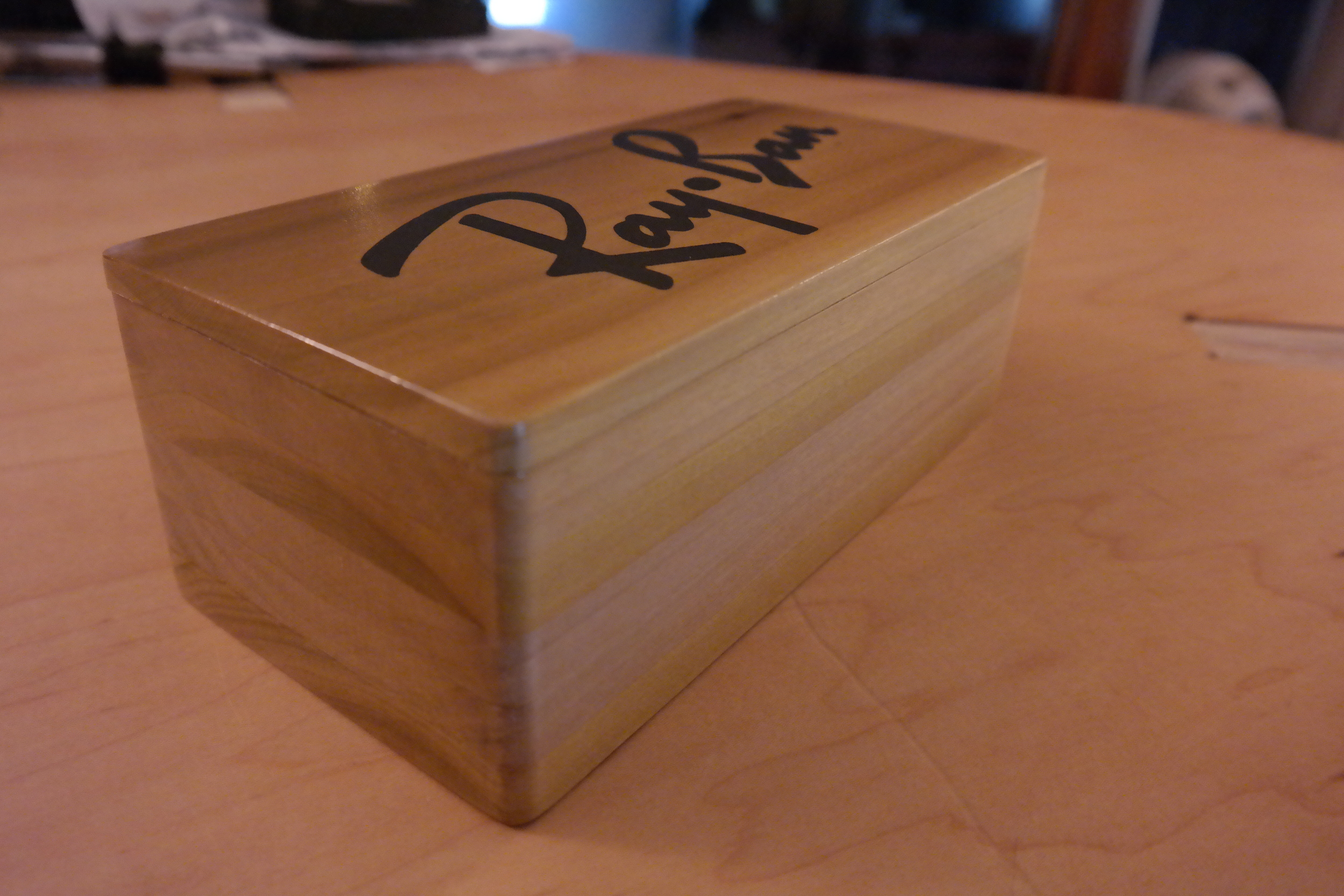
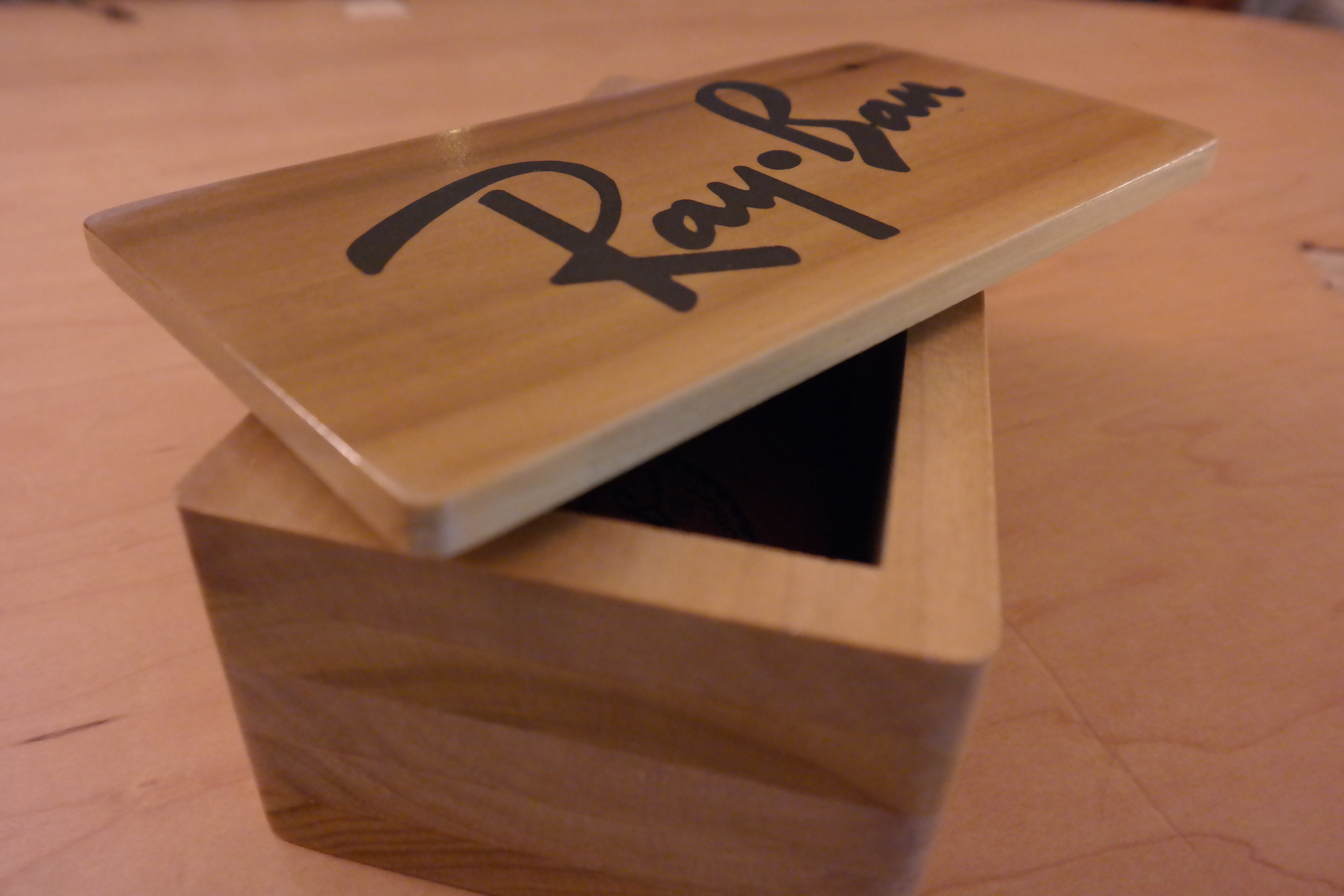
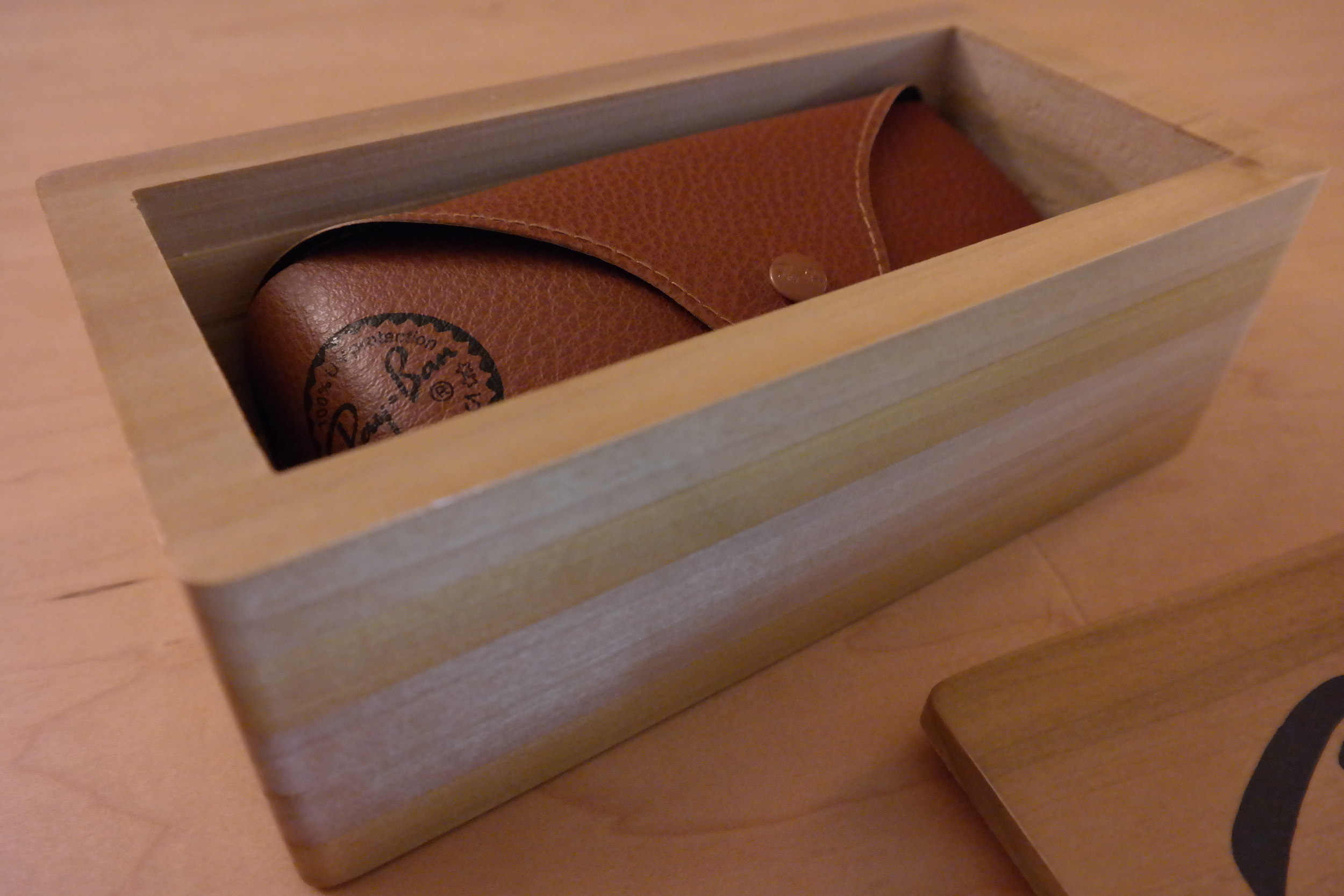
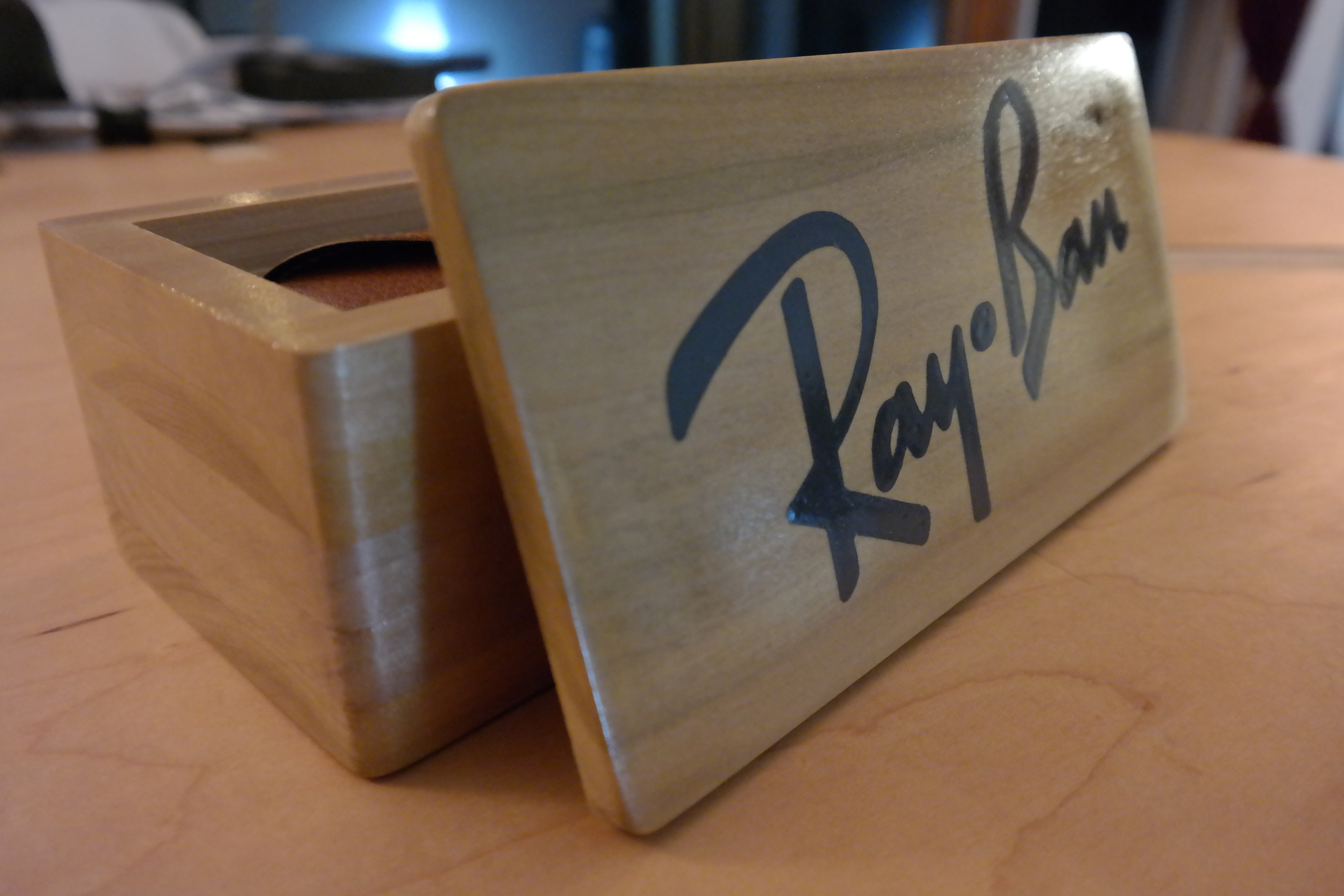
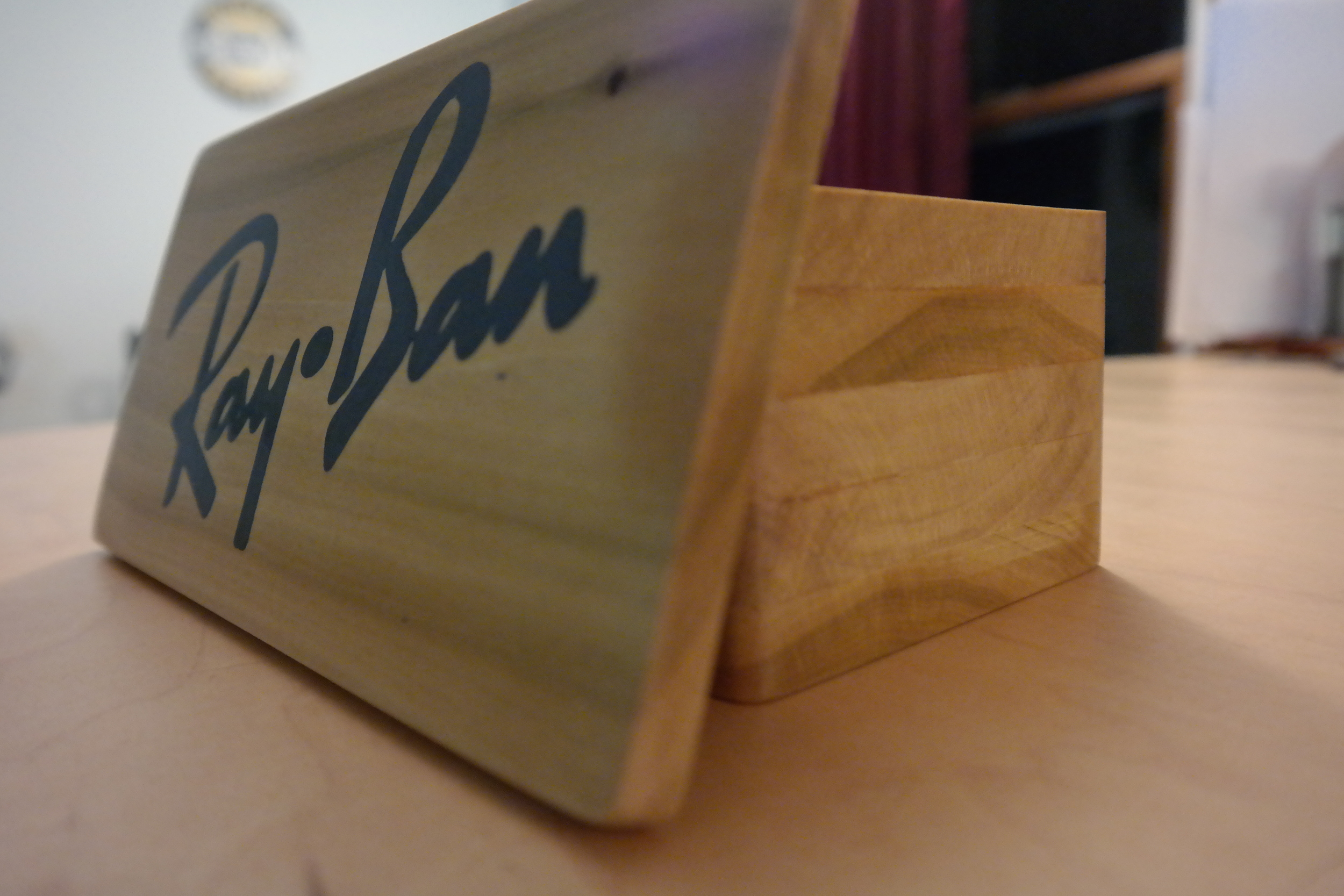

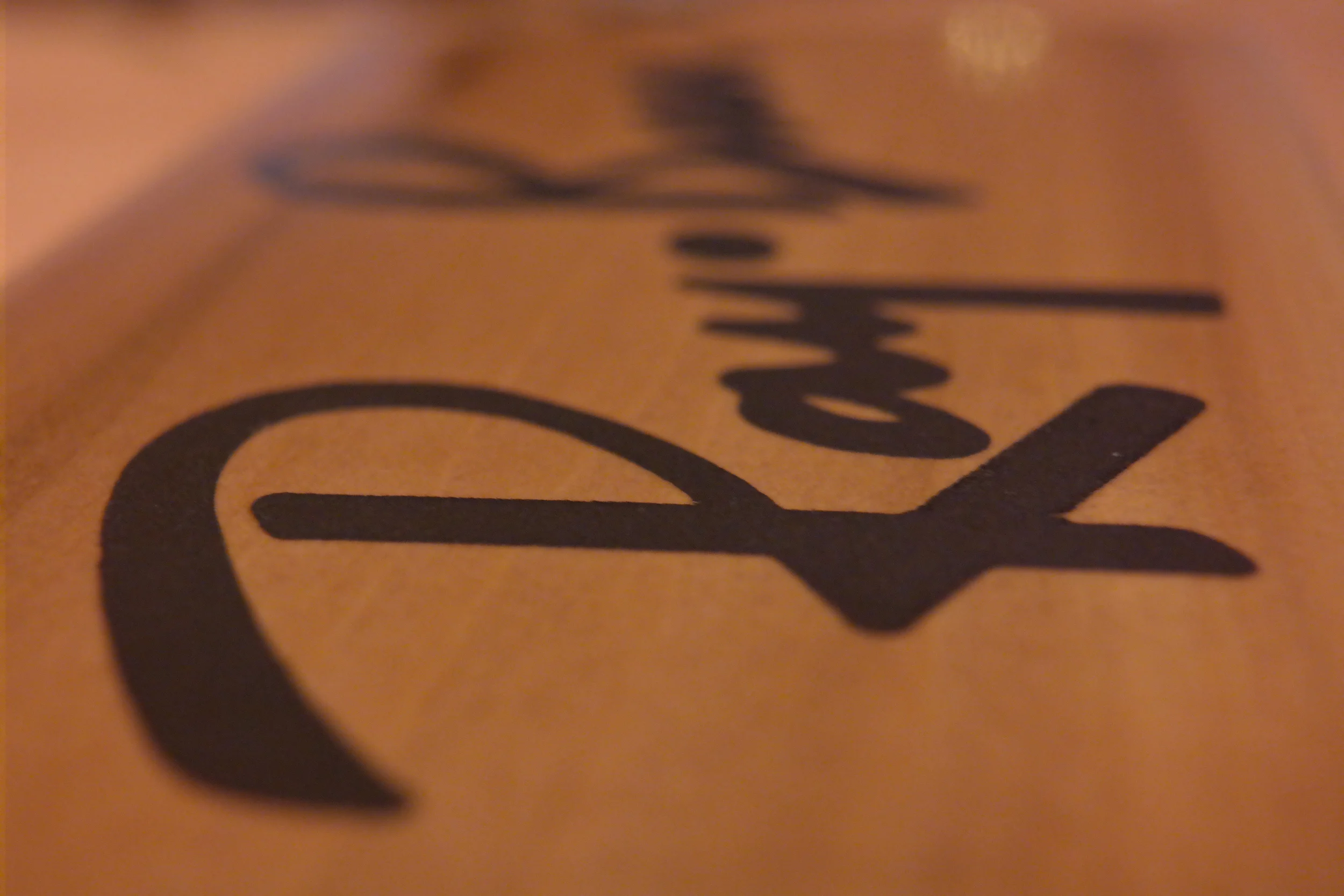
I have included the cutting files below. It should be noted that the Sketchup model shows everything at 0 tolerance. If you cut this way, your top will fit so tight into the rest of the case. You can either hand sand it, or you can add some tolerance in the cutting file. I did the latter, but I did it in VCarve. Depending on the wood, humidity, bit type, etc the amount of tolerance can vary. I find that .02" works pretty well. Test on some scrap to be sure before you commit to using finished wood.
The download here includes images, Sketchup files, and VCarve cutting files. Go mill it and let me know how you did!